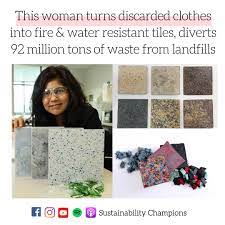
When China announced a ban on the importation of 24 types of solid waste in January 2018, the inherent inefficiency of Australia’s A$15 billion waste industry was suddenly exposed. An annual average of 619,000 tonnes of Australian recyclable materials were left without a home. The nation was facing a waste crisis, but Professor Veena Sahajwalla had a strategy for tipping the materials straight back into the economy.
As founding director of the Centre for Sustainable Materials Research and Technology (SMaRT) at the University of New South Wales (UNSW), Sahajwalla is revolutionising recycling science in collaboration with industry. Last year, she was appointed director of the NSW Circular Economy Innovation Network, which brings together stakeholders from across government, industry and research organisations to develop new processes and supply chains for reducing waste and improving sustainability.
In 2003, Sahajwalla invented polymer injection technology (PIT), known as green steel.
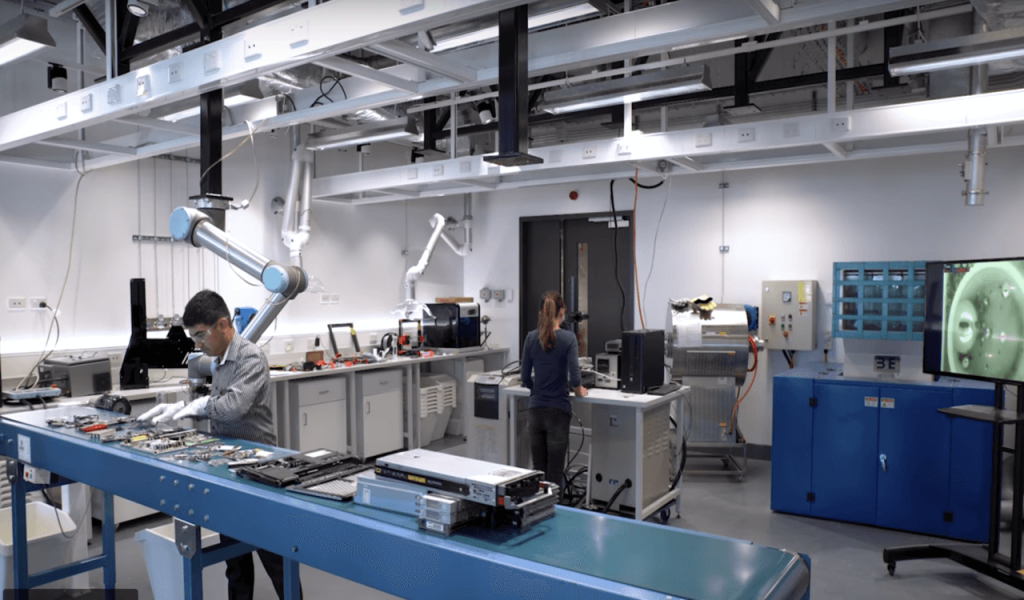
An environmentally friendly and cost-effective process for using recycled rubber tyres, the technology has been licensed to steel makers globally, and Sahajwalla and her team are working with Newcastle-based steelmaker MolyCop, which plans to implement the technology across its global operations.
In 2018, Sahajwalla launched the world’s first e-waste microfactory, where valuable metal alloys are extracted from discarded smartphones, laptops and circuit boards. Now she’s converting waste materials, such as the glass, plastic and textiles Australia previously exported or sent to landfill, into industrial-grade ceramics inside a second microfactory. She also plans to roll out her microfactory model across the country and, ultimately, the world.
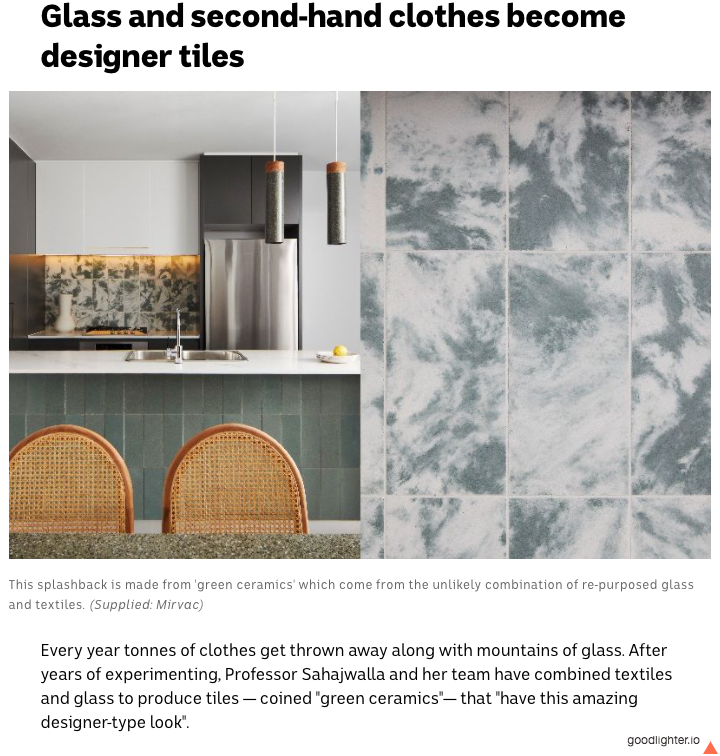
Capturing value in waste
Sahajwalla grew up in Mumbai, where she says waste was viewed as an opportunity rather than a problem. Rubbish heaps were trawled for plastic, cardboard and other materials of value to sell on to scrap dealers.
“The sense of repurposing and reusing, and sharing was driven by economic necessity, of course, but people were more than happy to have hand-me-downs, whether it was clothes or furniture items,” Sahajwalla says. “We would rarely throw away things that were in decent working order.”
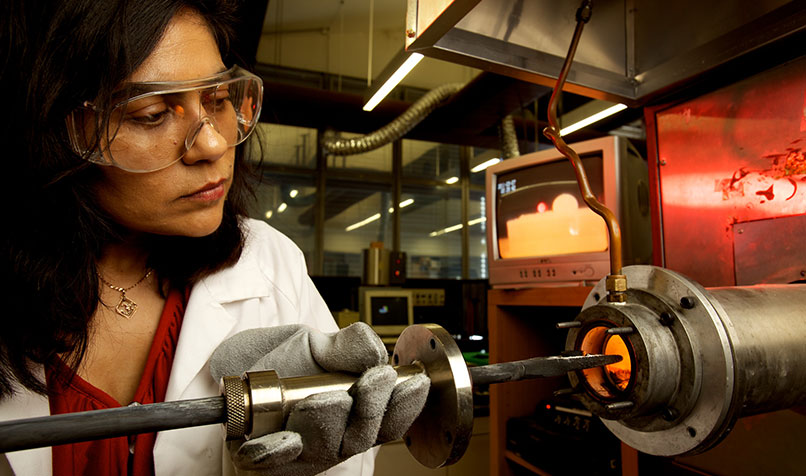
While Sahajwalla’s mother is a medical doctor, her father was a civil engineer, and she loved visiting his construction sites to see how things were built. “A Cadbury factory was my favourite,” she recalls. “When I think about it now, it was probably just an office building rather than an actual factory, but when you’re a kid and you see the symbol of Cadbury, making and how they got the liquid chocolate to become that solid slab and all the challenges there must have been to get it right.”
That early interest in materials science led Sahajwalla to study engineering at the Indian Institute of Technology, where she was the only woman in her class. She went on to earn her master’s degree at the University of British Columbia and, while completing her PhD at the University of Michigan, she was offered a job at Australia’s national science and research agency, CSIRO.
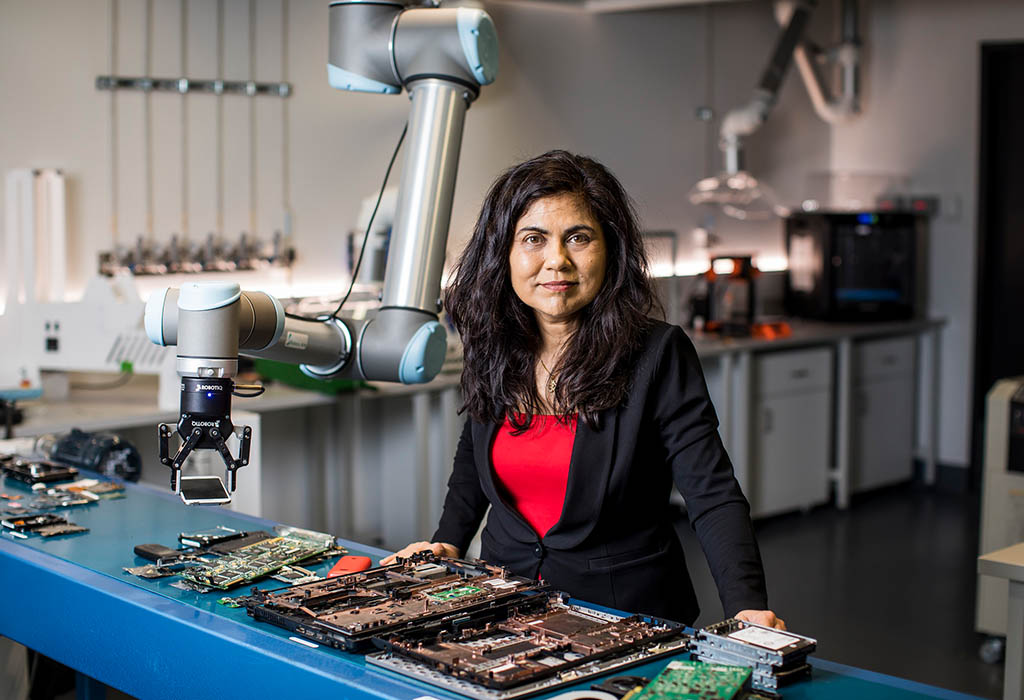
Sahajwalla’s stint at the CSIRO led to an academic position at UNSW, and it was in one of the university’s laboratories that she pioneered her green steel technology.
In Australia, 50 million vehicle tyres reach the end of their life each year, and only 16 per cent are recycled. Sahajwalla’s technology involves melting down carbon-rich rubber tyres to replace some of the non-renewable coke in the production of steel.
Rubber is cheaper than coke. It also creates less waste, which represents a cost saving to industry.
When rubber is transformed into smaller molecules in a furnace, millions of rubber tyres have been diverted from landfill thanks to Sahajwalla’s innovation.
“When we talk about recycling, it’s generally about converting like for like – converting a plastic bottle into another plastic bottle, for instance – but this is quite limited,” Sahajwalla says.
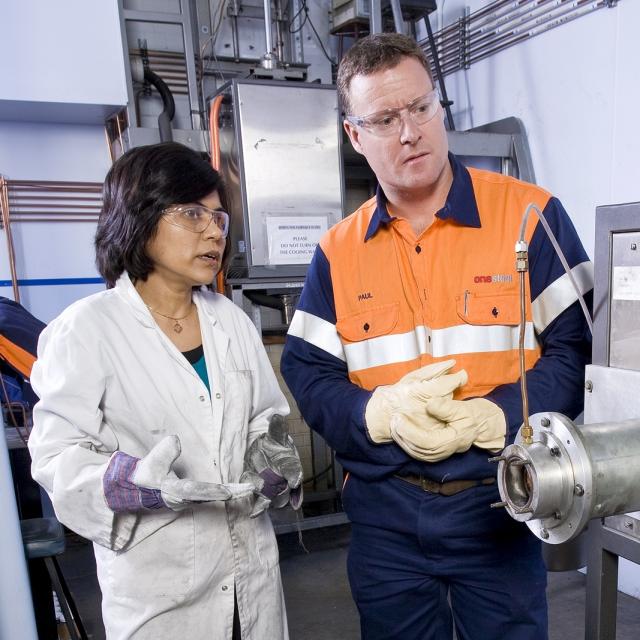
“Old tyres are no longer roadworthy, so they can’t be reused as tyres. What if you can see that old tyre as a collection of molecules that can be transformed and used in other manufacturing solutions?”
In 2005, Sahajwalla won the prestigious Eureka Prize for her green steel invention and, while she describes it as a “wonderful outcome”, the scientific recognition was not enough. “I wanted to use the research outcomes to create sustainable industry practices,” she says. “I needed to be able to show the steel industry that the benefits were not just environmental, but also economic.”
Fast-forward over a decade, and she has visited countless manufacturing centres across the country to promote the environmental and economic benefits of green manufacturing. She says engaging with the business community has been vital to getting her innovations to market. “We need scientific collaborators,” she says. “We also need [industry] partners who are open to trying new products and seeing the benefits in the longer term.”
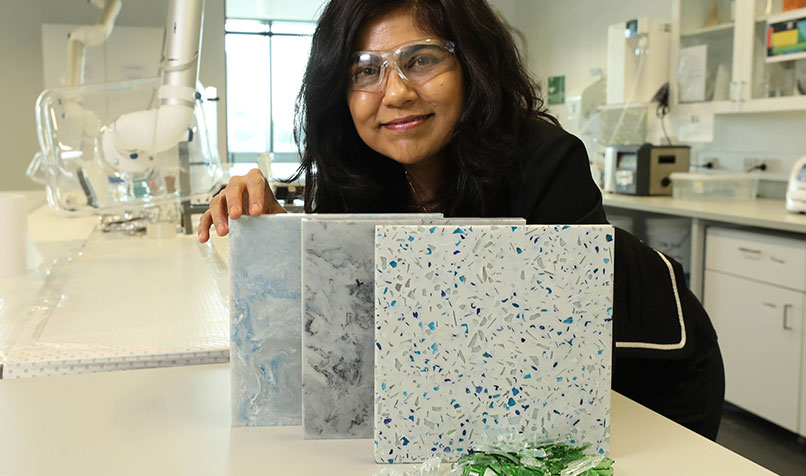
Many of these new manufacturing technologies are being developed via Sahajwalla’s unique microfactory model.
Microfactories feature a series of small machines and devices that use patented technology to perform one or more functions in the reforming of waste products into new and usable resources. They can be installed in an area as small as 50-100 square metres, and can be set up wherever waste is stockpiled, such as a building site or alongside regional waste disposal sites, to process waste at the source.
Sahajwalla says the microfactory model may disrupt the current highly centralised, vertically integrated industrial model.
“My model is one that is laterally integrated to allow different operators in the supply chain to connect,” she says. “If you can localise your solution, you’ve actually enabled everybody across the country to benefit by enhancing our manufacturing capabilities.”
The first microfactory was launched at UNSW with funding Sahajwalla received from the Australia Research Council (ARC), to convert electronic waste input into new products. Electronic devices are broken down and scanned by a robotic module to identify useful parts, which are then transformed into valuable materials. Computer circuit boards, for example, can be turned into valuable metal alloys such as copper, while plastics can be converted into filaments for 3D printing, which Sahajwalla describes as a “cost-effective” alternative.